A Pictorial Review
by
Ken & Trisha Brooks
This Baystate banjo (1865-1897), sold by John C. Haynes & Co., Boston; came into our store for repair of a broken peghead.
We thought you might like to see how the repair was done.
Click any picture for a larger view

The overlay wood was so dry that it crumbled while being removed. The inlay was saved to be put in the new overlay.
|

The front overlay piece had to be steamed & pried off.
|

The break glued and clamped.
|

The back view with a block screwed through peg holes for orientation of the new overlay. Keeps it from slipping while being clamped.
|

The new rosewood overlay glued and clamped.
|

The back stripe wood was also damaged and very dry. It will need to be filled with some pieces that were in a plastic bag in the case.
|

The new rosewood overlay had to be trimmed flush to the peghead.
|

Here you can see where the overlay needs to be trimmed to the curves and angles of the headstock.
|

The pegholes were drilled from the back through the new overlay then they were chamfered on the front side by hand using a countersink bit to fit the friction pegs.
|

Next the old inlay was traced onto the new overlay.
|

A hole has been routed using a fine bit in a Dremel router.
|

Clean hole cut to the depth of the old inlay.
|

The inlay is so thin that it had to be set to a perfect depth. There was no extra to sand down.
|

The inlay was glued & weighted.
|

And of course it had to be fille with this yucky business. Not to worry.
|
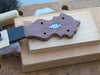
A little scraping & cleaning and it's good as new.
|

The dry and brittle wood of the back stripe was missing pieces. You can see some saved pieces in the plastic bag.
|

Some large pieces were glued in and taped until dry. More voids had to be filled with glue and ebony wood dust.
|

The nut was refit into the overlay at the proper depth.
|

The neck was taped off in preparation for staining the side of the peghead.
|

The overlay also needed stain.
|

The dry fingerboard was oiled to prevent cracking and fret protrusion.
|

The pegs being installed in their respective holes.
|

Time to put the parts back together.
|

The hardware securing the neck stick to the pot. All the shims were put back in place so the action would be correct.
|

The peghead side view of the repair
|

The finished peghead with a couple coats of lacquer for beauty and durability
|
This Baystate banjo is the first I've seen with a set screw built into the fifth string peg to keep it tight. Over the years, the hole had become enlarged and needed fixing so the screw would do its job.
|
A new set of strings and reattaching of a case hinge and this old timer is good to go.
|